In the waterborne coatings industry, achieving the desired coating quality and performance while optimizing production efficiency and reducing costs is an ongoing challenge. However, with the advent of mechanical equipment such as high pressure homogenizers, manufacturers now have a powerful tool at their disposal. This blog aims to explore the various applications and benefits of high pressure homogenizers in the waterborne coatings industry.
Homogenization and dispersion of pigments, fillers and materials:
High pressure homogenizers have proven invaluable in the waterborne coatings industry by homogenizing and dispersing pigments, fillers and other materials present in waterborne coatings. The homogenizer makes these materials subject to shearing, impact, peeling, etc. through the high-speed rotating cutter, which ensures the stability and uniformity of the coating. This in turn significantly affects the color, gloss and coat thickness of waterborne coatings.
Dispersion and emulsification of adhesives:
Another important application of high-pressure homogenizers lies in their ability to disperse and emulsify binders in water-based paints. This process greatly improves the adhesion and consistency of coatings, making them easier to apply, dry and cure. Enhanced adhesion and consistency ultimately aid in the use and durability of waterborne coatings.
Homogenizing and Dispersing Additives:
In addition to pigments and binders, additives also play an important role in determining the specific properties of waterborne coatings. Here, the high-pressure homogenizer shines again with homogenizing and dispersing additives, which improve properties such as corrosion protection, wear resistance and high-temperature elasticity. This versatility enables manufacturers to customize coatings to meet specific requirements and industry standards.
Benefits and future prospects:
The application of high pressure homogenizers in the waterborne coatings industry offers many benefits. By enhancing coating stability, uniformity and special properties, these machines help manufacturers consistently produce high-quality coatings. In addition, the adhesion and consistency of waterborne coatings are improved, which increases the ease of application, drying and curing, which positively affects the overall use and durability of the finished product.
In addition, the efficient operation of the high-pressure homogenizer directly contributes to the improvement of production efficiency. By reducing batch times and reducing the need for additional equipment, manufacturers can streamline processes and increase output. Furthermore, as production costs decrease, firms can allocate resources to other areas of innovation and growth, thereby enhancing market competitiveness.
In conclusion, high pressure homogenizers have become valuable assets in the waterborne coatings industry. Their ability to homogenize and disperse a wide variety of materials and improve adhesion, consistency and specialty properties is critical to achieving best-in-class coatings. By increasing production efficiency and reducing costs, High Pressure Homogenizers are key players in the industry for excellence and cost-effectiveness. As the technology advances, we can expect further advancements leading to wider applications in the future.
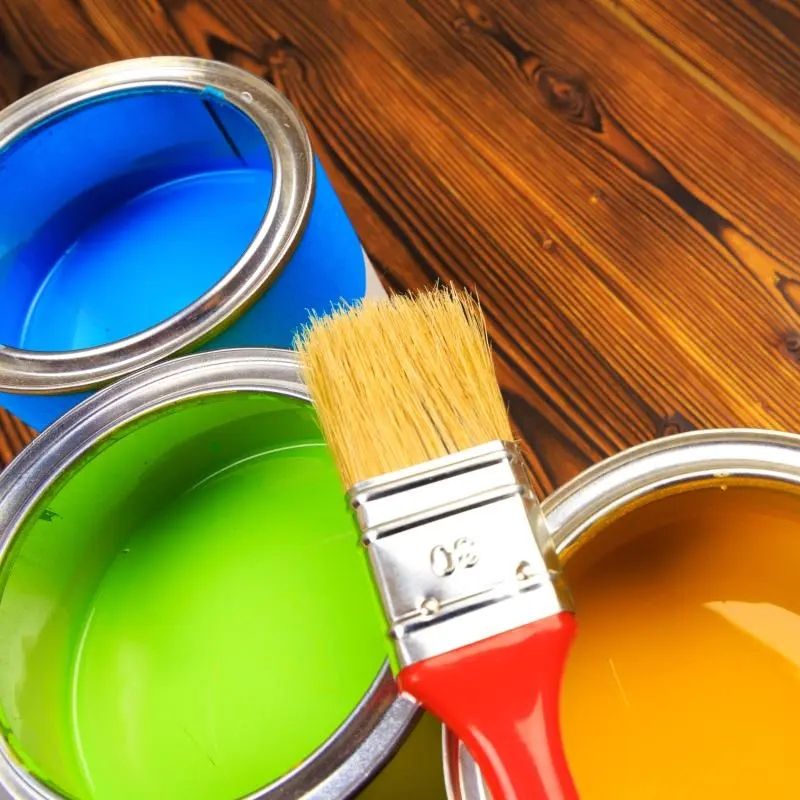
Post time: Sep-06-2023